Finite Solutions
High Quality Casting Simulation Software at a Reasonable Price
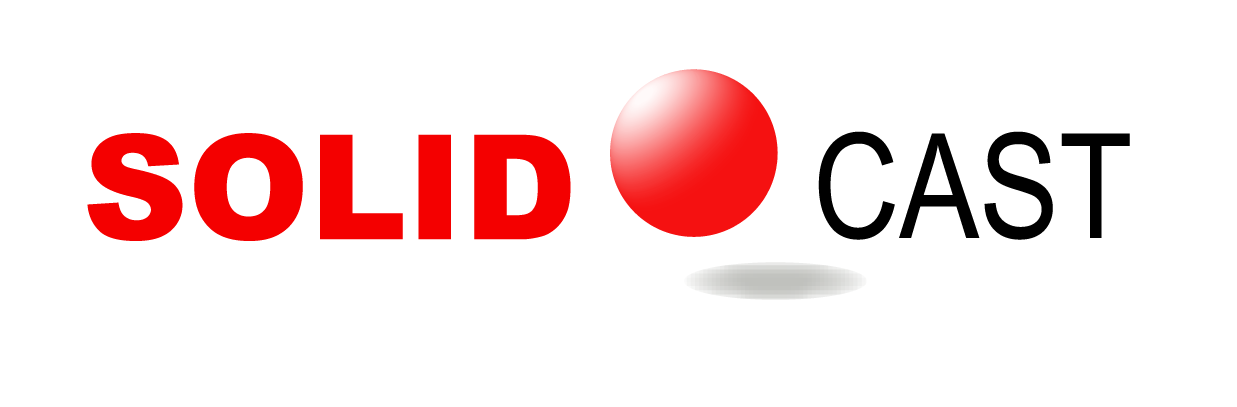
SOLIDCast lets you see how castings will solidify before making pattern equipment, dies and costly mistakes. Pour test castings on the computer, not on the foundry floor! No other casting modeling program offers power, ease of use and accuracy like SOLIDCast!
Learn More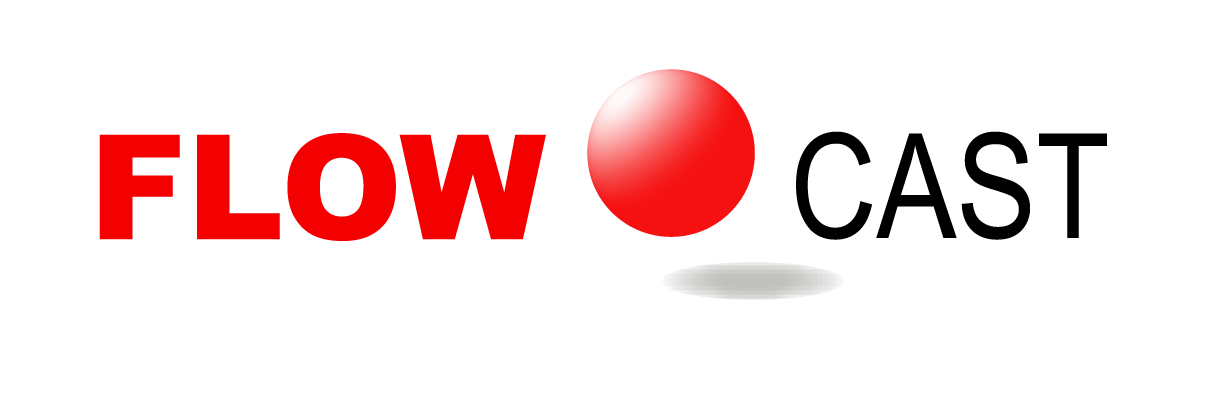
FLOWCast, a full-featured CFD (Computational Fluid Dynamics) simulation of flow, is based on solution of the Navier-Stokes equations for fluid flow. With FLOWCast, users can view progressive temperature, fluid velocity and fluid pressure during the fill, from any angle of view.
Learn MoreThis system of tools provides:
Accurate Design
The ONLY system that includes both Gating and Riser Design Wizards, so that simulation actually helps users design an effective rigging system, not just test one.
Casting Made Easy
SOLIDCast has many features to make simulating in any gravity-fed process a snap. Our software fine tunes simulations for sand casting, permanent mold, and investment casting.
Precise Simulations
SOLIDCast is the ONLY system that simultaneously calculates both thermal and volumetric changes during solidification, producing the most accurate shrinkage analysis available. Run full simulations in minutes, on readily-available standard PCs.